At Protecnic we are specialists in mould making, that is, in generating the moulds that manufacturers need to give plastic a certain final shape depending on the type of industrial processes they apply and the products they need to produce.
In this sense, two of the most common technologies when working with thermoplastics are injection moulding and extrusion. For this reason, our team is capable of manufacturing injection moulds and also plastic extrusion moulds.
How are they similar and how do they differ? They are similar in that they are industrial parts intended for the manufacture of products and that they can all be created using the numerical control machining centres we have at our facilities in Castalla.
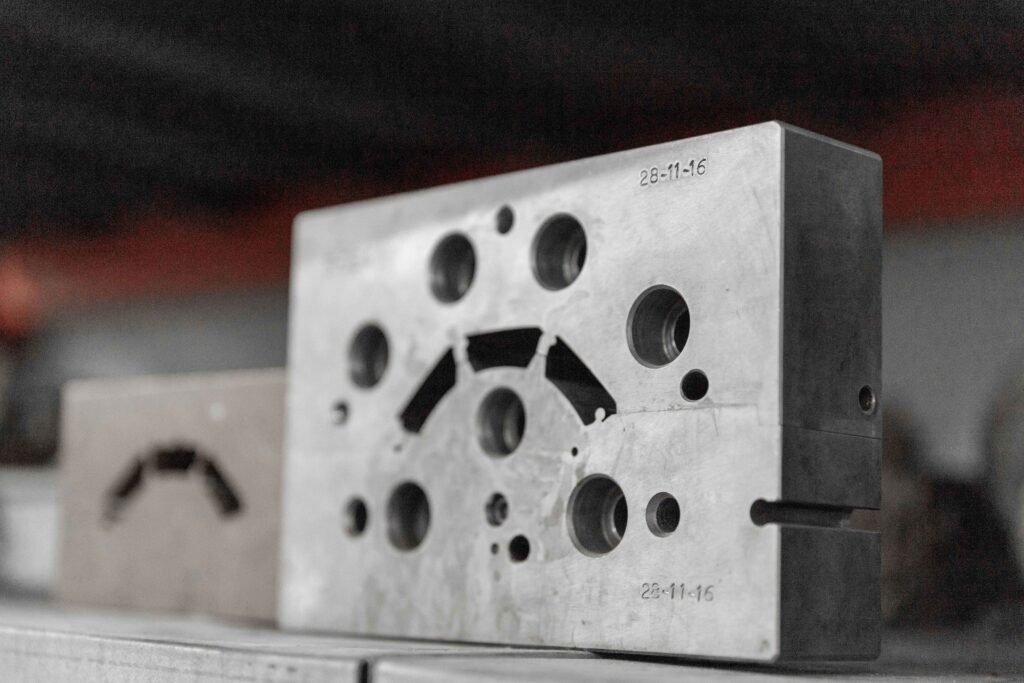
The main difference is that in the case of extrusion, an inlet and outlet hole is required in the mould to facilitate the moulding of the material. These plastic extrusion moulds can be used to produce continuous strips of products such as our PVC ABS edgebands sample book., special profiles and tambour doors to create cabinet doors, to name but a few.
But there are many more options. From connecting profiles for tables to other solutions known as 'bubble profiles', which are used to cushion the closing and opening of doors.
Inside the mould, the entry and exit points are shaped according to the desired product. The finished product is then cut to the desired size.
In the case of injection moulding, this requires closed, airtight moulds with a hollow interior. This inner hollow has the exact silhouette that the final part must adopt. Once the moulded part is finished, a plunger or piston pushes the heat-softened plastic into the mould. Given its fluid state, the polypropylene manages to reach the interior of the mould, which is cold, where it adopts the predetermined shape.
After a short time, due to the temperature change, the plastic solidifies. The mould can then be opened and the piece can be removed. We have recently collaborated on projects of this type with furniture manufacturers such as Kassani and its Albert, Federico Giner and his Dida chair and Actiu, with its the TNK Flex professional chair..