After cleaning, sorting, or mixing, recycled plastic waste or other raw materials are extensively processed using a plastic extruder. This substance is frequently extruded into filaments that can be used as a starting point for further processing by being chopped into bead or pellet stock.
Extruders are more frequently employed while processing polymeric polymers. The plastic is melted, processed, and then re-melted. These resins often come in the shape of beads or pellets, allowing for their usage in extrusion equipment. The plastic pellets are forced into the extruder and onto the processing screw by a hopper. PVC is by far the most popular plastic extruder, while others include those for polyethylene, polypropylene, acrylic, polystyrene, polyamides, polystyrene, acrylonitrile butadiene styrene (ABS), and polycarbonate.
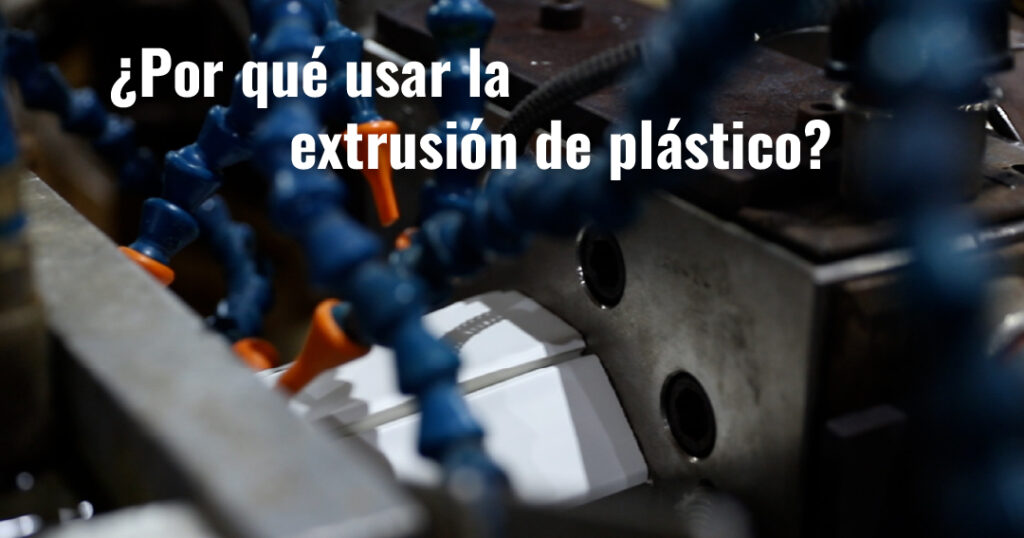
The price of a plastic extruder is not set in stone and is determined by a variety of factors. It is dependent upon the material to be processed and the calibre of the extruders' components, such as the screw or barrel. Moreover, the screw's length might also affect the cost of downstream machinery or specialised accessories for particular raw materials.
In order to make pipes, profiles, pellets, or medical devices, extrusion machines push or pull unused material into alignment guides and shaped dies. Extrusion is frequently employed in the plastics sector and offers economic advantage as well as flexibility and the possibility to be customizable. Moreover, standard goods like pipes and profiles can be produced using the high-volume manufacturing process of extrusion.
The production of small and large-size moulds for plastic extrusion and injection is a key component of Protecnic's history. We are experts in the habitat industry and collaborate with the top furniture manufacturers, also with their product divisions and the industrial designers they hire to come up with the ideas for their catalogues. It is because of our partnership with all of them, we are able to define the industrial solutions that match their designs and their conception of the finishes.
To obtain exact results, design, engineering, manufacturing, and product require a coordinated and cohesive approach. At Protecnic, we offer experience in tooling and technical solutions.