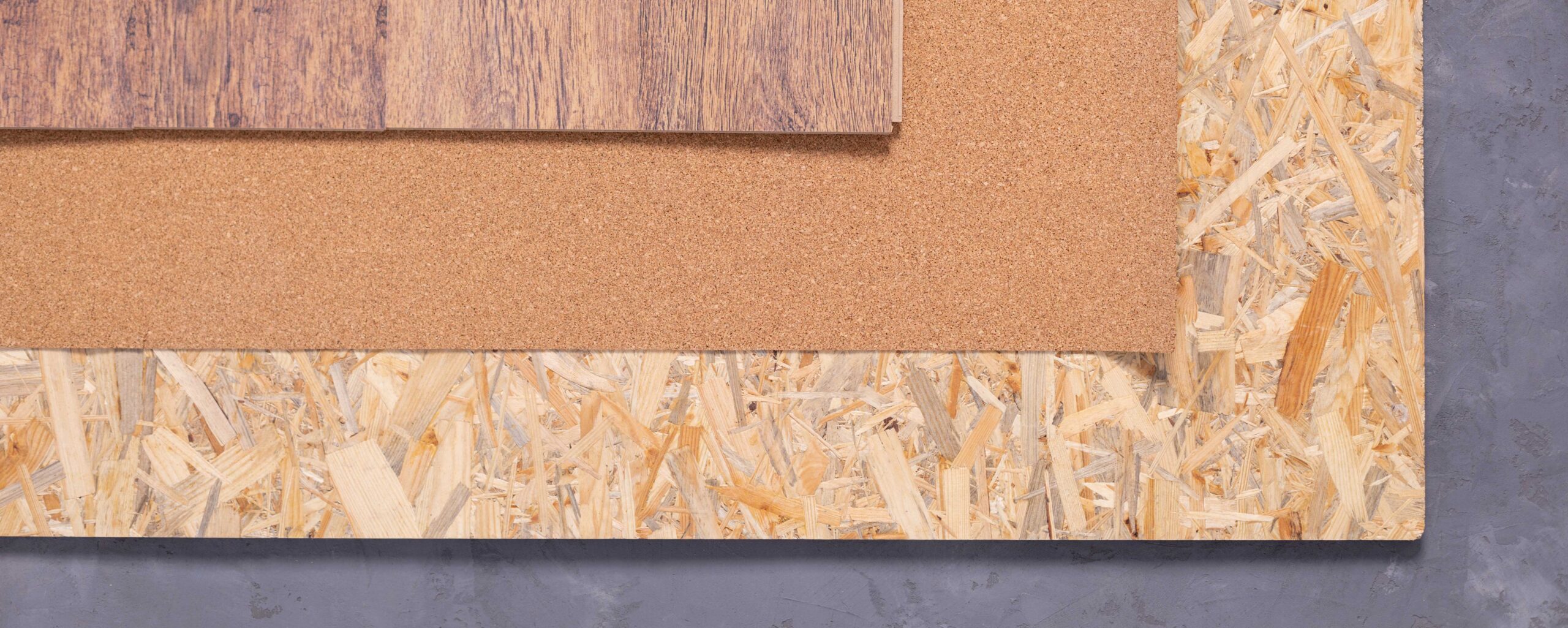
It is common to mention the melamine boards as a whole in which the only differences were their color, size and design. But the melamine, is only refined to the surface, the printed top layer that gives the board a greater durability over time and, also, a characteristic apparence.
The board can be manufactured in differents forms to generate various qualities. The most common options are MDF and chipboard.
MDF boards are also known as: Medium Density Fibreboard, DM, Trupán o Fibrofácil.
They have in common both are versatile, resistant and easy to maintain. Furthermore, both options are abtained from extracting and pressing the wood fibers at a temperature of around 200ºC.
The difference is in the density of the particles that make up each board. In the case of chipboard, these wood particles are joined in two layers while, in MDF, they are connected themself.
It allows the MDF boards to be more resistant and ductile. Its exterior is more porous and smooth, which makes it an excellent surface to be laquered. It is a solid Surface so it favors the adherence of differents types os glues and achieves the appearance of solid wood. It is used on tables and shelves, among other pieces of furniture.
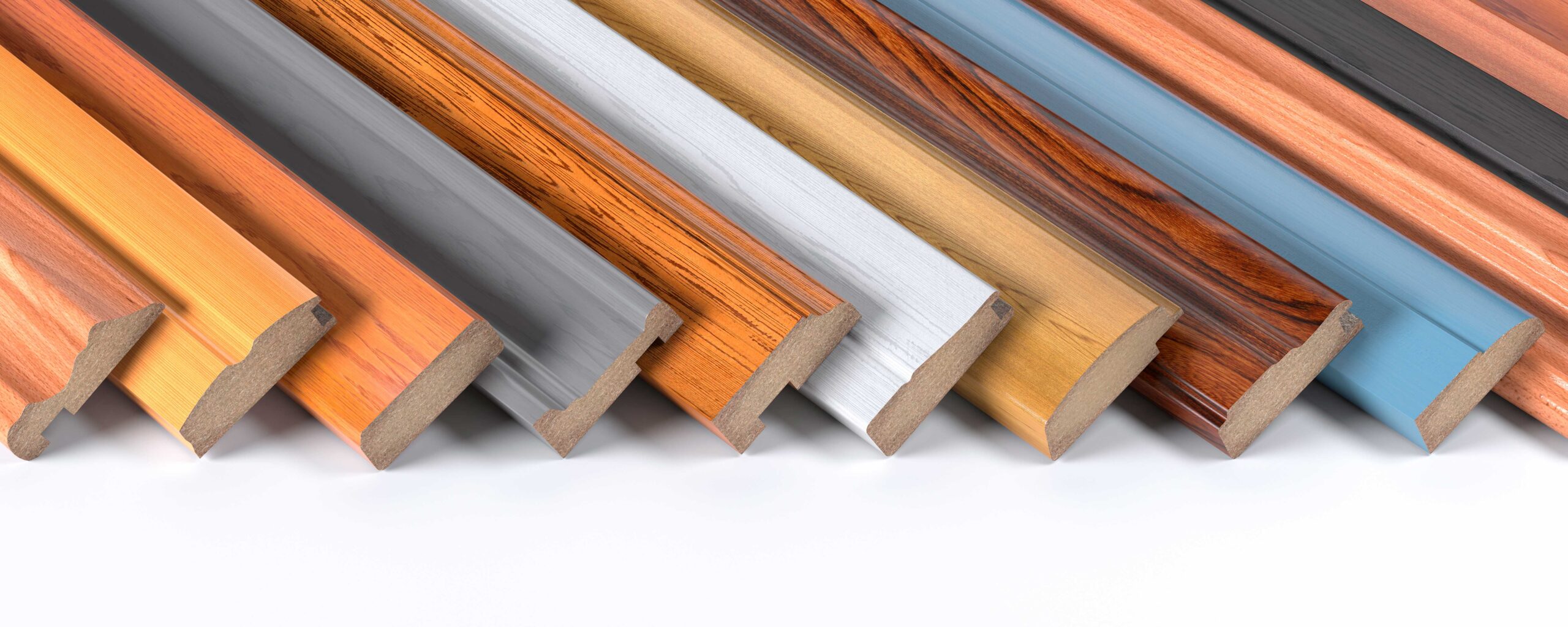
On the other hand, the boards created from chipboard are stiffer and lighter, with a rougher surface, and are commonly used for doors, drawers and shelves. They are also cheaper.
Both MDF and chipboard can be coated with plastic resins also known as “melamine” that can emulate the features of different types of woods designs, colors and finishes.
All boards are marketed in similar dimensions, although there are varieties like those resistant to fire and humidity impact. These qualities are achieved by incorporating certain chemical compounds at the board manufacturing process.
At Protecnic, we are specialists in solutions for the furniture sector for more than two decades. We make color matches for all types of melamine boards, adjusting our different processes (extrusión, decor, varnish, etc.) to the silhouette, design and needs of each project.
Our catalogue of references PVC ABS edges adds more than 5,000 finishes and it grows every month, side by side with the new designs of the board manufacturers and the specific requirements of the companies for which we work.