Extrusion molding is a process in which a stack of powders is pushed into a die to assume another form or other final product under pressure. This process is also known as plastification extruding, and is used to manufacture pipes, hoses, drinking straws, curtain racks, rods, edgebands, and fibers.
Para crear una estructura larga en forma de “tubo”, los gránulos se funden en un líquido y se empujan a través de una matriz. La forma del tubo viene determinada por la forma de la matriz. Tras enfriarse, la extrusión adquiere una forma sólida. El tubo puede cortarse a intervalos iguales e imprimirse sobre él. Los componentes pueden embalarse juntos o enrollarse para su almacenamiento. El cable de fibra óptica es uno de los productos más conocidos del moldeo por extrusión. Podemos decir que el moldeo por extrusión es comparable al moldeo por inyección, diferenciándose en que se produce una forma larga y continua, para que resulte más sencillo de entender.
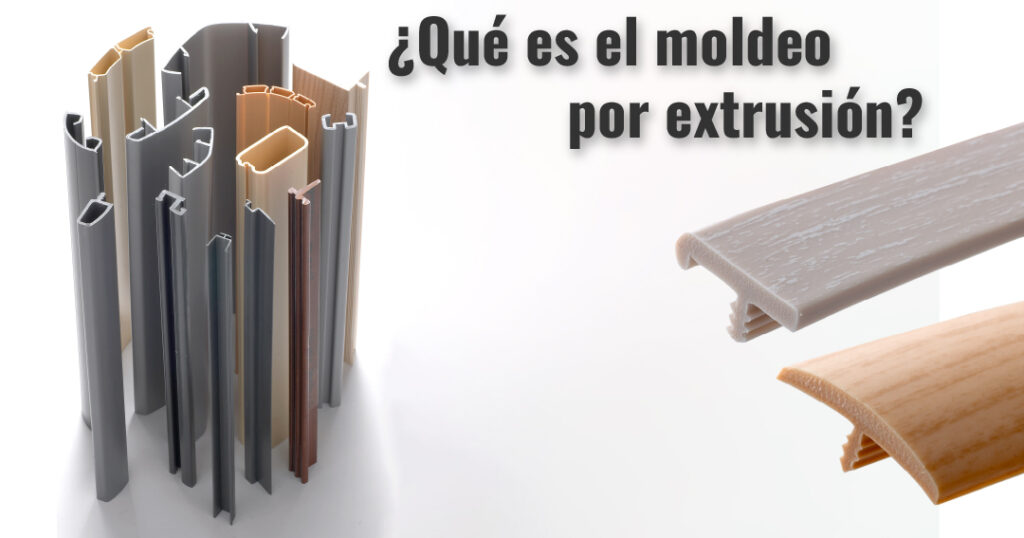
Extrusion molding is done at low temperatures, typically between 40 and 200 ºC, the cold extruding process is used to remove the green body from mixes of metal powders and organic binders. Preparing the material, preprocessing, extruding, cutting, and reforming are some of the steps.
The characteristics of a material are significantly influenced by plasticizers. As a result, they must meet a number of criteria, including the necessity to be removable, sticky, and to have a high capacity for pore formation during sintering without reacting with porous materials. Olefin, amylum, and polythene alcohol are the most frequently used plasticizers. In addition to the usual compression caused by the extrusion shaft, powders will also experience pressure from the side wall, friction between the powder and the wall, or friction between the extrusion shaft and the wall.
The types of powders, the shape and size of the particle, the type and content of the plasticizer, the accuracy of the mold, the pressure from extrusion, the speed of extrusion, and the preheating temperatures are the main variables impacting the properties of extrusion molding. Depending on the best plastic to use with the chosen plasticizer at the chosen temperature, the preheating temperature is chosen. Experimental analysis can be used to gauge the extrusion speed. Additionally, it has a close connection to the plasticizer, fluidity, extrusion ratio, fluid particle size, and shape. The final piece could crack at faster extrusion molding rates.